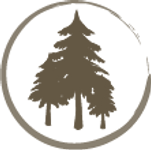
NANALTECO, S.L.ENVIRONMENTAL CHEMISTRY
MOF, Catalysts, CO2 removal
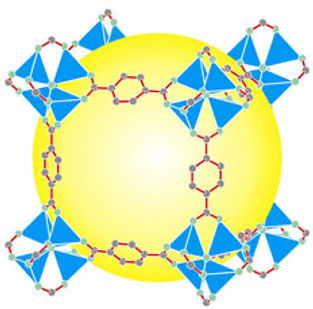
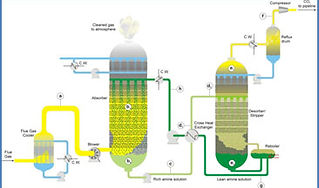
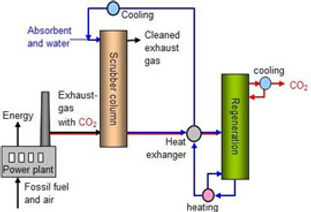




MOF
In order to tailor the optimal MOF structure for each particular case, a genetic algorithm that efficiently optimizes a desired physical or functional property of (MOFs) by evolving the functional groups within the pores will be used. With their nanoscopic pores and incredibly high surface areas, MOFs are excellent materials for gases separation. MOFs’ vast internal surface areas allow them to hold remarkably high volumes of gas. The volume of some MOF crystals might be the size of a grain of salt, for example, but the internal surface area, if unfolded, could cover an entire football field. The approach will be used to optimize the CO2 uptake capacity relevant for post-combustion CO2 capture. A total search space can have millions of structures to reach exceptional CO2, having their CO2 adsorption increase by more than 5 times.
PROJECT TITLE: UPGRADING HEAVY OIL RESIDUES AND ASPHALTENES
The high potential of the research group led by Prof. Leonid Kustov related to both preparation of catalytic nanomaterials and their application in hydroprocessing of heavy hydrocarbon feedstock, including both individual hydrocarbons (long-chain paraffins, polycyclic molecules) and asphaltenes has been demonstrated. Extremely efficient catalysts based on free-standing and
supported metal nanoparticles, including cheap non-noble metal nanoparticles) have been designed and used for the hydroconversion of asphaltenes into the light hydrocarbon pool via the simultaneously occurring reactions of hydrogenation, hydrogenolysis, ring opening, and hydrocracking. As a result, a rather high conversion of asphaltenes (up to 80%) was achieved,
while in the case of individual substrates the conversion reached 100%. The only drawback of these original and fascinating materials is the necessity of using hydrogen for the conversion, occurring usually at elevated pressures. A dream catalyst would be equally efficient in the absence of hydrogen under ambient pressure. Unfortunately, Mother Nature sets some limits (either kinetic or thermodynamic) that cannot be bypassed even by inventive minds. Such a
dream performance, in principle, can be achieved, however, at the expense of lower catalyst stability and necessity of frequent regenerations, which is not unusual and rare in the industrial practice (for instance, short-time catalytic cracking with an 8 seconds active cycle and 8 seconds regeneration). In some cases, the use of sacrificial catalysts (Approach I) that are not regenerated may be considered as a robust and even green approach, if cheap components are
used in the catalyst (natural carriers, non-expensive metals like Fe). Thus, good perspectives of nano-engineered supported and unsupported metal, oxide or sulfide nanoparticles in the efficient conversion of heavy oil and asphaltenes into light products can be demonstrated. The use of structured carriers and structured catalysts (Approach II), for instance, based on metal foams, gauzes, sintered metal fibers or foils with supported components is another option to enhance the efficiency of asphaltene converting catalysts in a flow mode of operation. Of special interest are the catalysts containing cheap metals, such as Co, Fe, Ni, Ru applied in the reactions of cracking and ring opening of heavy molecules present in asphaltenes. Hydrogen in the composition of asphaltene can serve for internal hydrogenation, thus excluding the use of external hydrogen supply. The accessibility of the active metal sites to the bulky molecules present in heavy oil and asphaltenes is the crucial issue, therefore, the proper arrangement of
metal, oxide or sulfide particles, the choice of the carrier, the size, and morphology of the particles are of utmost importance. The recent studies carried out at Nanalteco with a sample of asphaltene obtained from a Russian vendor showed the principal viability of the proposed approaches: the nanocatalysts of diverse nature of nanoparticles (metal NPs, oxide NPs, and sulfide NPs) suspended in asphaltene melt or solution in an appropriate aromatic solvent (xylene)
are capable of converting crude asphaltene into light products by cracking / ring opening mechanisms. By doing so, they can reduce the normalized viscosity of asphaltene approximately twice without using hydrogen. The gel-penetration chromatography method showed the decrease of the average molecular weight, polydispersity as indicated below:
For the starting asphaltene:
M N = 597.409
M W = 2061.98
Polydispersity index M W /M N = 3.45154
Molecular mass of the maximum peak: 742.737
For the product mixture obtained after the treatment of asphaltene:
M N = 359.54
M W = 949.36
Polydispersity index M W /M N = 2.640485
Molecular mass of the maximum peak: 320.35
However, the high pressure is still required (the preliminary experiments were performed in an autoclave at 20-30 atm), but exclusively to prevent evaporation of the solvent (if used, i.e. xylene) and light products formed (typically in the C7-C15). A principally different approach can be applied when CO 2 is used as a reactant causing disintegration of asphaltene components into lighter molecules (Approach III). The possibility of such a reaction was recently demonstrated by the team of Prof. Kustov by using lignin or brown coal, in this case, gasification occurred according to schematic equations:
C + CO 2 = 2 CO
C n H m O x + CO 2 → CO + H 2 + H 2 O
Further conventional Fischer-Tropsch catalyst can be used to convert the mixture into hydrocarbons or carbonylation processes can be arranged downstream.
Thus, the goal of the project is to develop an improved nanocatalyst with enhanced activity/selectivity helping to improve the oil flow by targeting a viscosity of 500 cP or lower. Tests with heavy oil or asphaltenes are conducted in (1) a batch reactor in the liquid phase or (2) in a down-flow reactor with structured catalysts being fixed on the shelf in the reactor.
Process parameters include:
Pressure of 1-50 bar, but preferably close to 1 bar
Temperature 200-400 o С.
Contact time – variable
H 2 supply – none
Heavy Oil samples are characterized before and after catalyzed cracking / ring opening treatment
at Nanalteco facilities:
- Aromatic vs non-aromatic hydrocarbon content (including chemical analysis) using spectroscopy (e.g., IR, NMR) and MS-GC;
- Viscosity measurements;
- Density measurements;
- Refractive index measurements
- Gel-penetrating chromatography
Nanalteco is interested in the partners to jointly develop the catalysts and processes, including commercialization of the technology.